Comprehending Porosity in Welding: Exploring Causes, Effects, and Avoidance Methods
As specialists in the welding market are well conscious, comprehending the reasons, effects, and prevention strategies related to porosity is important for accomplishing robust and trusted welds. By delving right into the root triggers of porosity, examining its detrimental results on weld quality, and checking out reliable avoidance methods, welders can enhance their expertise and skills to produce top quality welds consistently.
Typical Reasons of Porosity
Contamination, in the type of dirt, oil, or corrosion on the welding surface, creates gas pockets when heated up, leading to porosity in the weld. Improper securing happens when the securing gas, frequently utilized in processes like MIG and TIG welding, is unable to fully secure the molten weld swimming pool from responding with the surrounding air, resulting in gas entrapment and succeeding porosity. In addition, inadequate gas insurance coverage, usually due to wrong circulation prices or nozzle positioning, can leave parts of the weld unguarded, enabling porosity to form.
Results on Weld Quality
The presence of porosity in a weld can substantially compromise the general top quality and integrity of the bonded joint. Porosity within a weld develops gaps or tooth cavities that damage the framework, making it extra vulnerable to cracking, deterioration, and mechanical failure. These gaps serve as stress concentrators, lowering the load-bearing ability of the weld and enhancing the possibility of premature failing under used tension. Additionally, porosity can additionally act as possible sites for hydrogen entrapment, additional aggravating the degradation of the weld's mechanical buildings.
In addition, porosity can hinder the performance of non-destructive testing (NDT) strategies, making it testing to spot other problems or gaps within the weld. This can lead to significant safety and security worries, particularly in essential applications where the architectural integrity of the bonded parts is paramount.
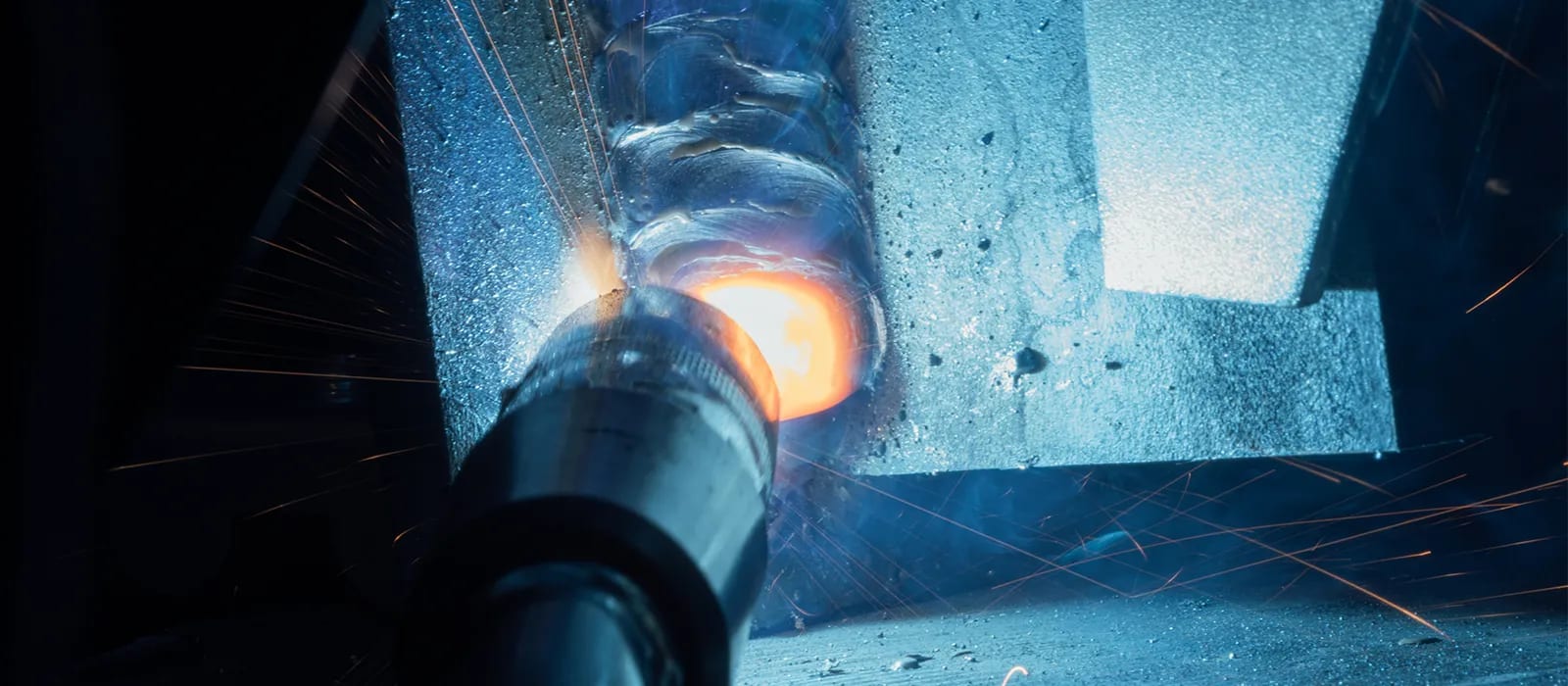
Avoidance Techniques Introduction
Provided the destructive effect of porosity on weld high quality, reliable avoidance techniques are vital Visit This Link to maintaining the structural honesty of welded joints. In addition, selecting the proper welding criteria, such as voltage, existing, and take a trip rate, can help lessen the risk of porosity formation. By including these prevention techniques right into welding methods, the event of porosity can be considerably reduced, leading to stronger and extra dependable bonded joints.
Relevance of Correct Shielding
Appropriate shielding in welding plays a crucial duty in avoiding climatic contamination and making certain the honesty of bonded joints. Securing gases, such as argon, helium, or a combination of both, are commonly used to secure the weld swimming pool from reacting with elements airborne like oxygen and nitrogen. When these reactive aspects enter into contact with the hot weld pool, they can trigger porosity, causing weak welds with reduced mechanical properties.

Insufficient securing can lead to various problems like porosity, spatter, and oxidation, compromising the architectural honesty of the bonded joint. As a result, adhering to appropriate securing methods is necessary to produce high-quality welds with marginal flaws and make certain the durability and reliability of the bonded parts (What is Porosity).
Surveillance and Control Methods
Just how can welders properly monitor and manage the welding process to ensure optimal results and prevent issues like see this site porosity? By constantly keeping an eye on these variables, welders can recognize variances from the suitable conditions and make immediate modifications to prevent porosity development.

Additionally, implementing correct training programs for welders is vital for keeping track of and controlling the welding process effectively. What is Porosity. Educating welders on the importance of keeping constant specifications, such as proper gas shielding and travel rate, can aid prevent porosity concerns. Normal analyses and accreditations can likewise ensure that welders are skilled in tracking and managing welding procedures
Additionally, making use of automated welding systems can boost surveillance and control capabilities. These systems can exactly control welding criteria, minimizing the chance of human mistake and making certain consistent weld top quality. By incorporating innovative monitoring innovations, training programs, and automated systems, welders can successfully check and manage the welding process to lessen porosity defects and accomplish top notch welds.
Verdict
